
OVERVIEW
I am the SRAD Solid Propulsion Team Lead for Duke AERO! We are an Intercollegiate Rocket Engineering Competition team for the annual Spaceport America Cup (SAC). For the past 2024 year, our rocket "Pitchfork" competed in the 10k SRAD category, spanning 6 in. in diameter and over 10 ft. in height. Our motor featured an ammonium-perchlorate cuprous oxide propellant, showcased components machined in-house.
For the 2024 Spaceport America Cup, the team was awarded the Jim Furfaro Award for Technical Excellence in addition to scoring 1st for Design and Build and 4th for technical documentation.
Throughout this experience, some key skills I have demonstrated include:
•CAD design/hardware manufacturing proficiency
•Leadership and systems integration across multiple sub-teams
•CAD design/hardware manufacturing proficiency
•Leadership and systems integration across multiple sub-teams
For the upcoming year, my team and I are now working towards the development of an O-class solid motor for 30K SRAD category. Check back periodically for updates!
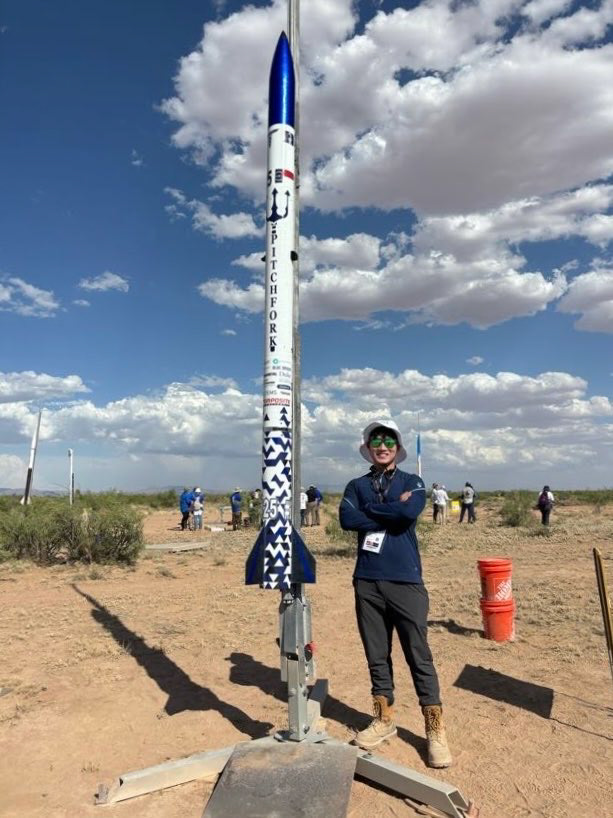
PROPELLANT FORMULATION AND TESTING
With 2024 being the team's first year competing in SRAD, we chose a propellant with a relatively low solids loading as well as a mild burn rate modifier. Resultantly, it could be less sensitive to changes in Kn, which allowed for error in the grain fabrication process given its novelty to the team.
Next, a testing session was conducted with the propellant formula and overall motor geometry. This test consisted of live-firing 8 H-class motors 38mm grains alongside a variety of nozzles to manipulate Kn so that we are able to see changes in ignition, impulse, chamber pressure and begin constraining the design.
The excitation of copper atoms from the cuprous oxide burn rate modifier results in visible blue wavelength emission, producing a satisfying blue flame. See the media on the right!
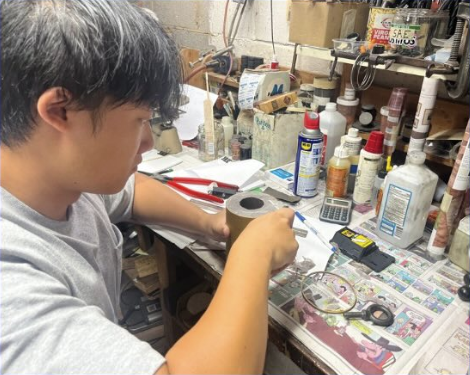
Afterwards, several critical values were calculated, allowing us to scale the data from the mini-motors and predict the behavior of the eventual 98mm full-scale motor, projected to generate nearly 700 lbf max thrust. The test files were then uploaded to BURNKNG, a student-developed Python optimizer that considers each test files' Kn and impulse per gram, and optimizes the best-fit curve to the data. By then sorting by residuals, the most optimal geometries were targeted for our motor design.
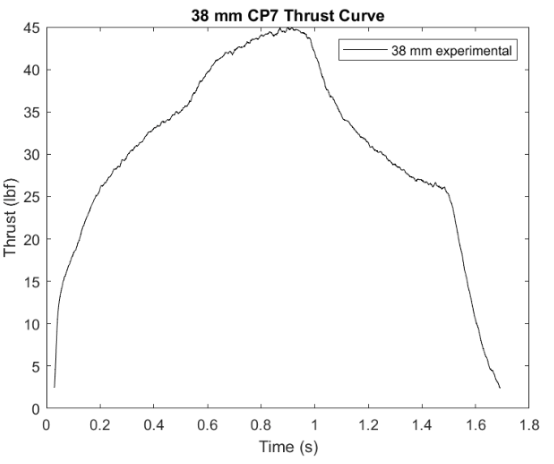
38mm Thrust Curve
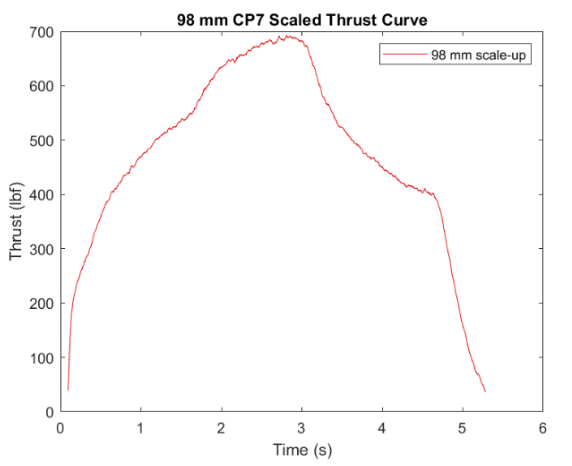
98mm Scaled Thrust Curve
HARDWARE DESIGN AND MANUFACTURING
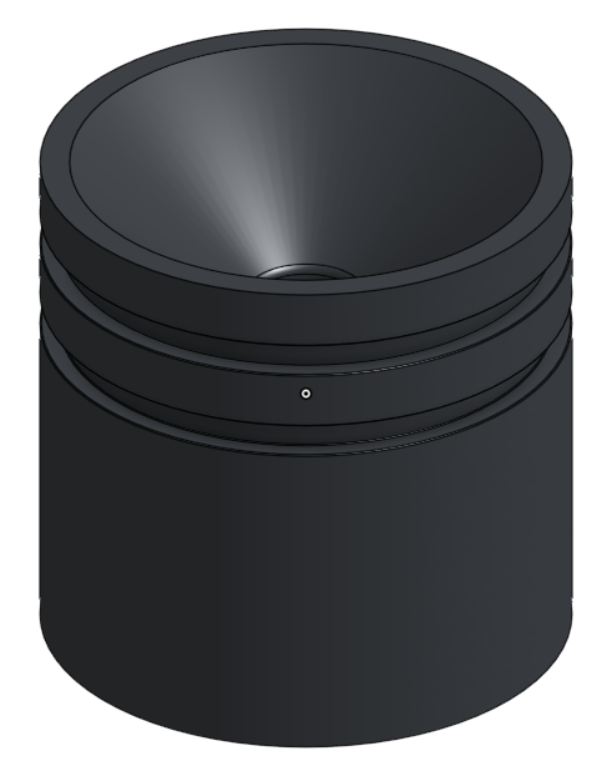
Nozzle Onshape Model
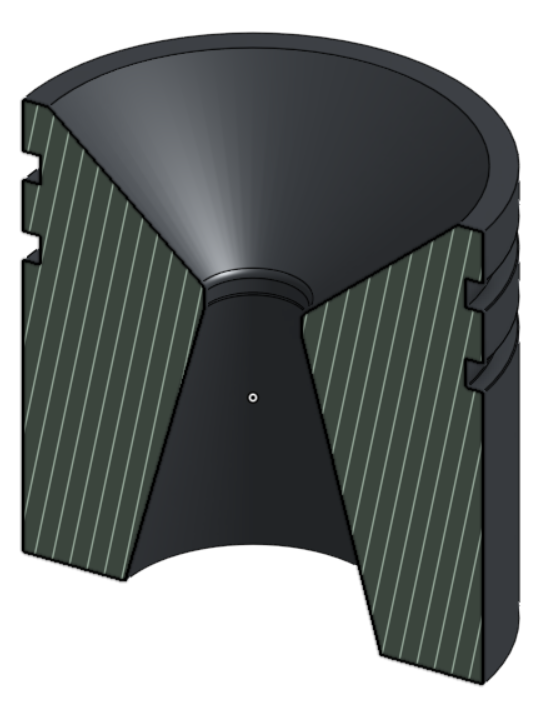
Nozzle Onshape Model (Cross-section View)
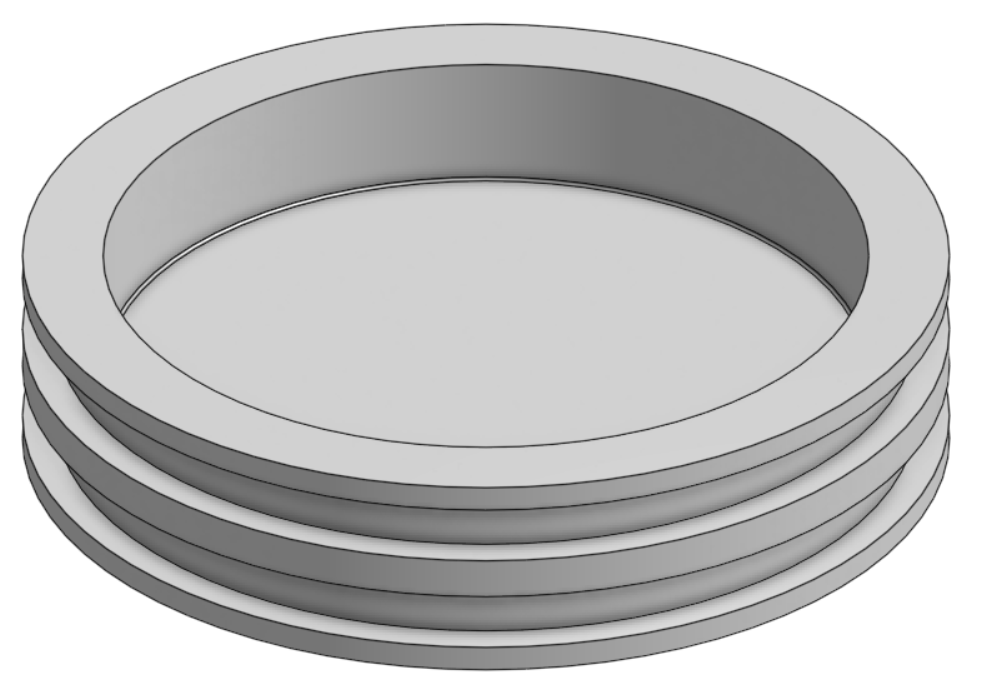
Forward Closure Onshape Model
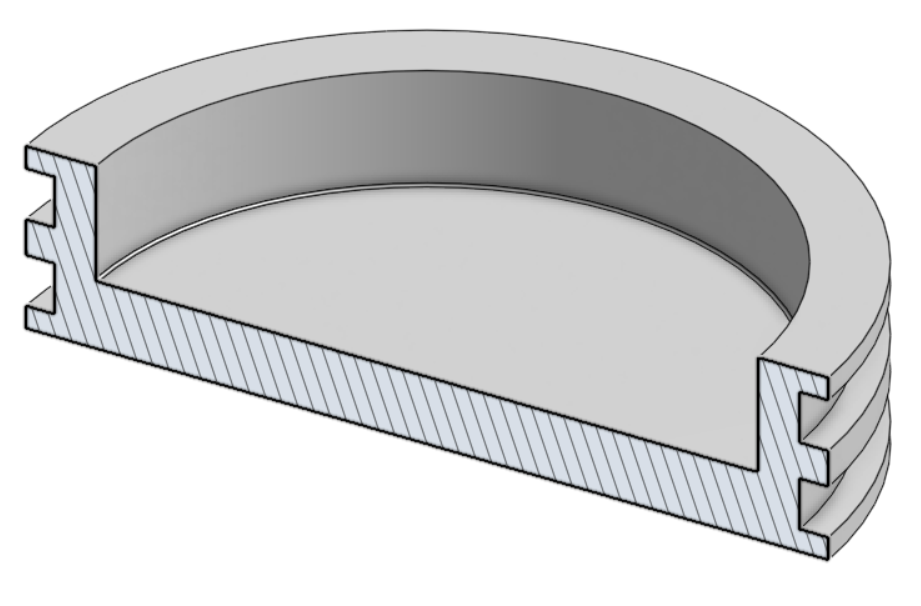
Forward Closure Onshape Model (Cross-section View)
With geometry roughly determined, the forward closure, nozzle, and case were ready to be designed and manufactured, needing to withstand high chamber pressures and have flexible models when other team situations change. After calculating stresses and factors of safety, the models were designed to take advantage of Onshape's driven variables, allowing for easy changes.
After all parts were specified and toleranced with O-ring grooves, all components were manufactured and the motor was ready for full assembly integration. With everything secure, the final case measures 27 in. in length and weighs ~15 lbs, housing four 6.5” propellant grains.

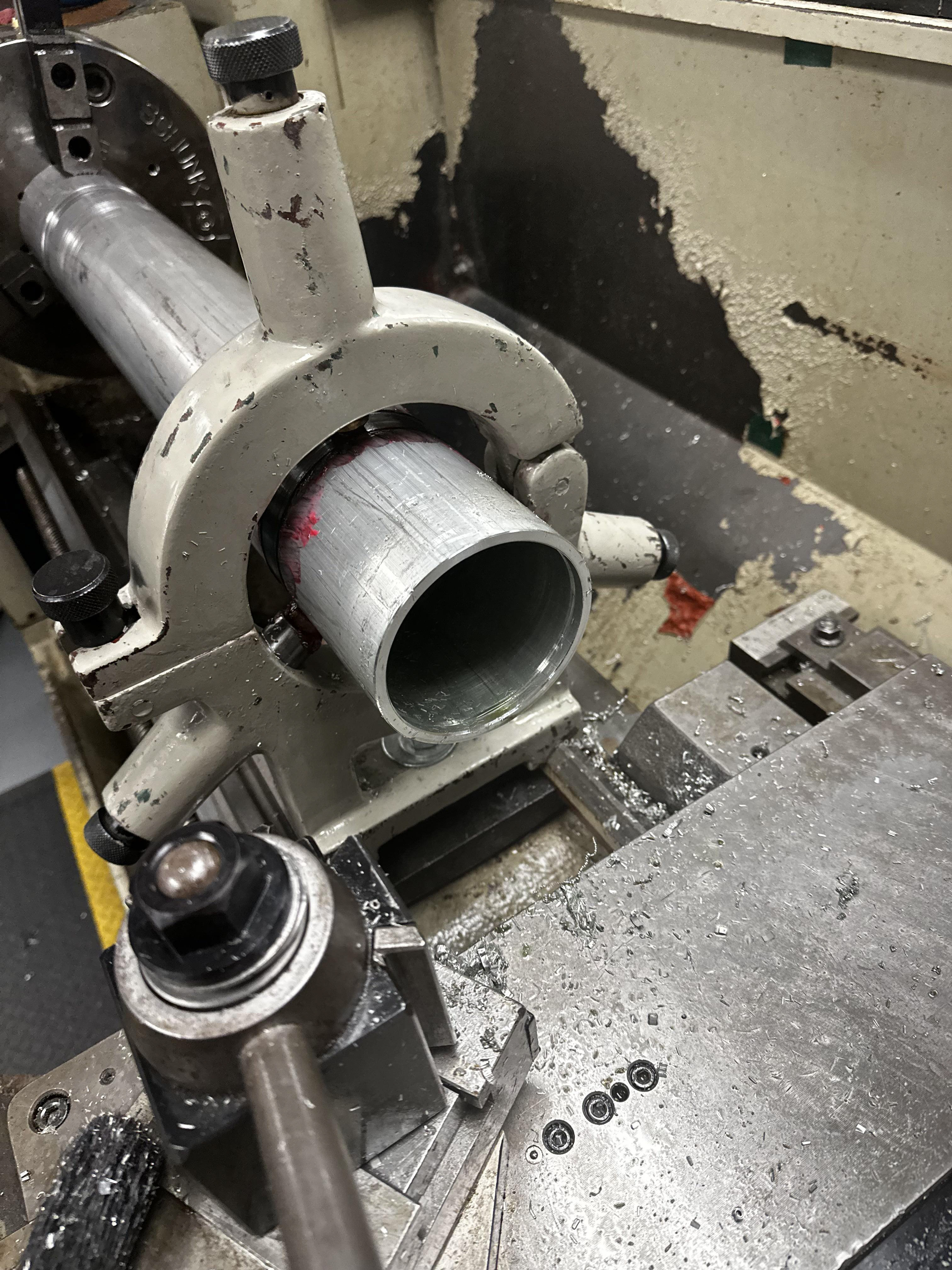
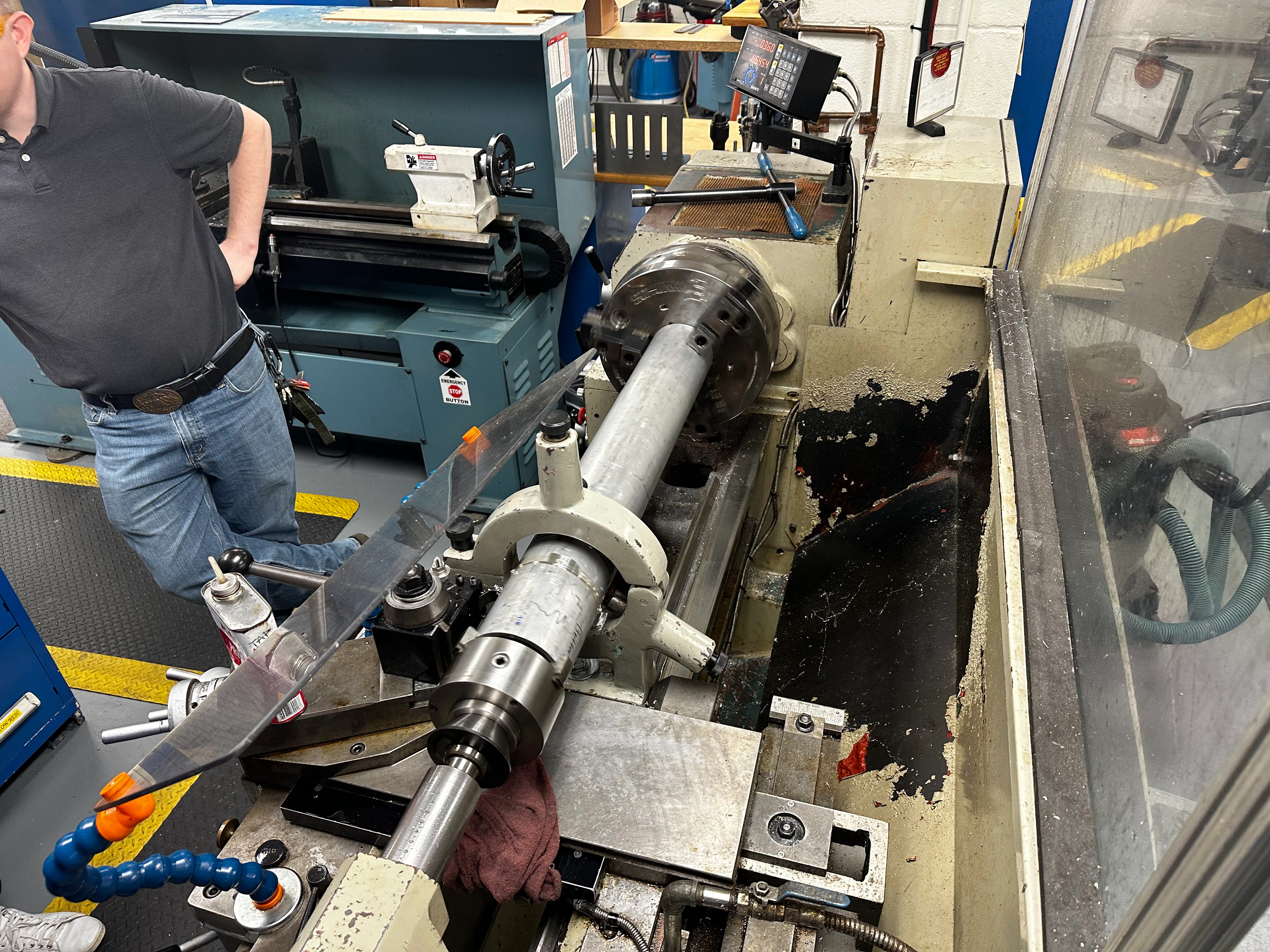
However, while machining the case, we ran into an issue: the stock was not acceptably circular, varying up to 0.04" with the indicator. To machine the case accurately, we first ensured that the tube was aligned by fixing the second chuck on the free end, held by a live center. We then machined wear bands on the outside of the tube to create a reference surface to indicate from and to set the steady rest on, using a rounded cutter to create a radius and lower excessive stress concentration. Next, the free end was faced off and chamfered, before using square insert to cut internal snap ring groove. This process was then repeated on other face, with the facing tool centered against chuck and using a dead blow hammer to minimize runout.
After the case was machined, a rough FEA on geometry was performed to examine unexpected addition of wear bands, which ensured that with 212 and 2500psi on the inner diameter, the minimum FOS was not on area of wear bands.
MOTOR TESTING
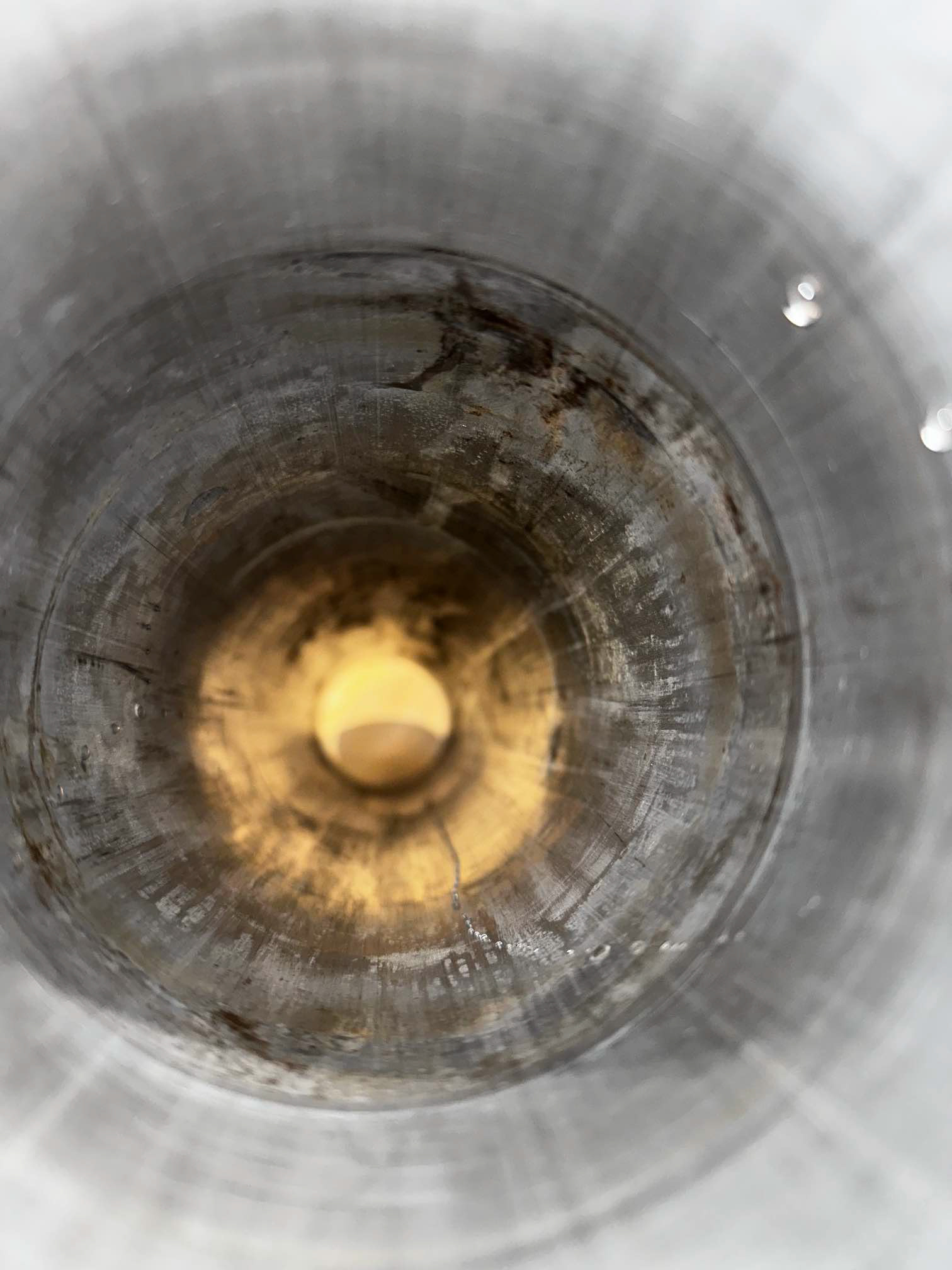
Aft-end of Case Post-fire
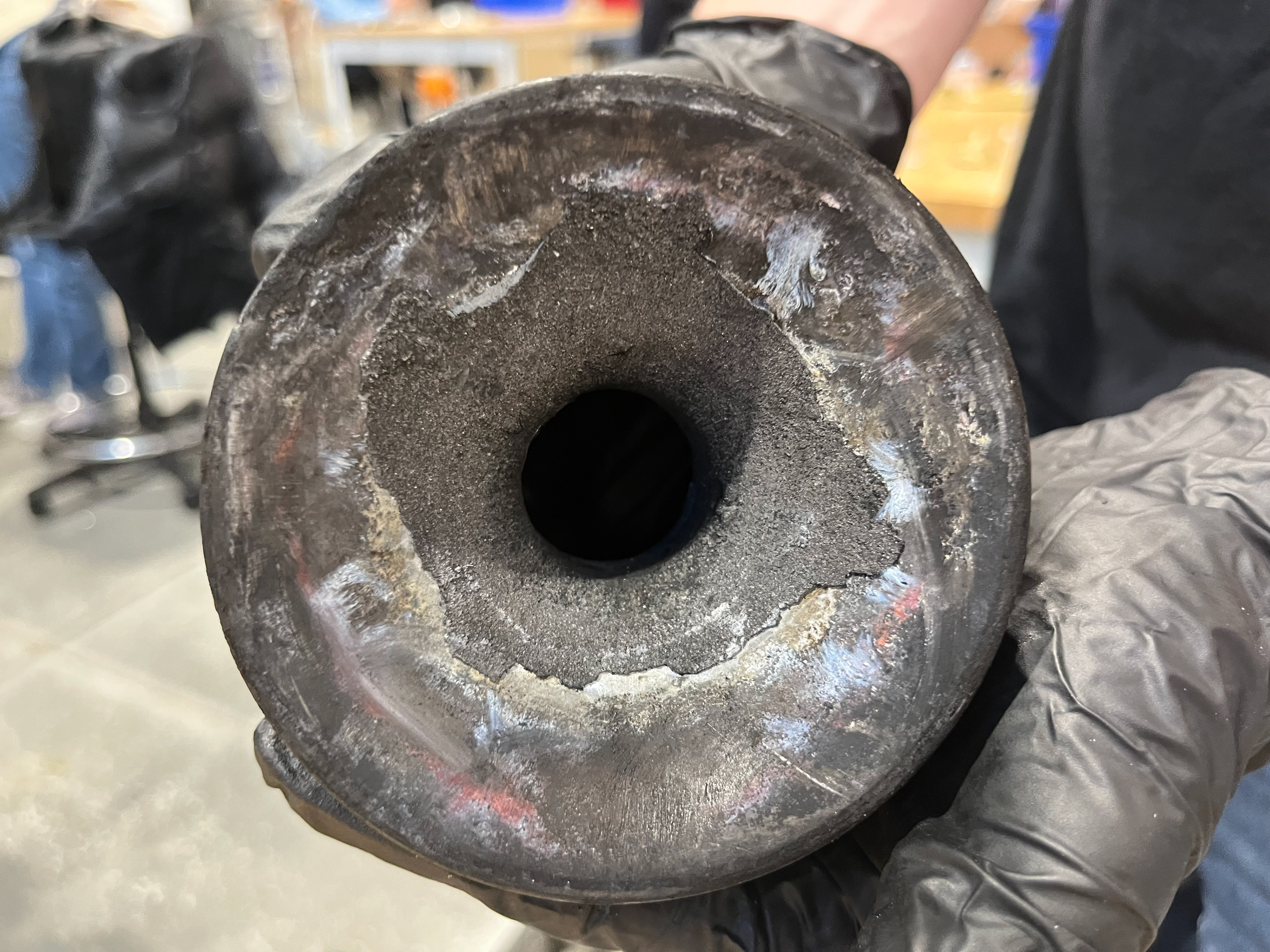
Nozzle Post-fire
Pressure-tapped Forward Closure (1)
Pressure-tapped Forward Closure (2)
After assembly, the full-scale motor was subjected to both hydrostatic and static hot-fire testing, attached with a pressure tap forward closure to measure data and compare with predictions. The motor was then connected to a load cell, which measured a total impulse of 2600 lbf*s and an average thrust of 620 lbf. See media above for hot-fire!
We also found BURNKNG to predict the actual impulse extremely accurately. The exact impulse generated by the motor was 11519 Ns (static hot fire later). This impulse was entered into BURNKNG which predicted a required propellant length of 23.15 inches -- a 0.06% percent error from the actual total length.
SPACEPORT AMERICA
Unfortunately, our launch at SAC had an early separation, causing a CATO shortly after launch. However, all components were successfully recovered, with most hardware with minimal wear.
For the 2024 Spaceport America Cup, the team was awarded the Jim Furfaro Award for Technical Excellence in addition to scoring 1st for Design and Build and 4th for technical documentation.
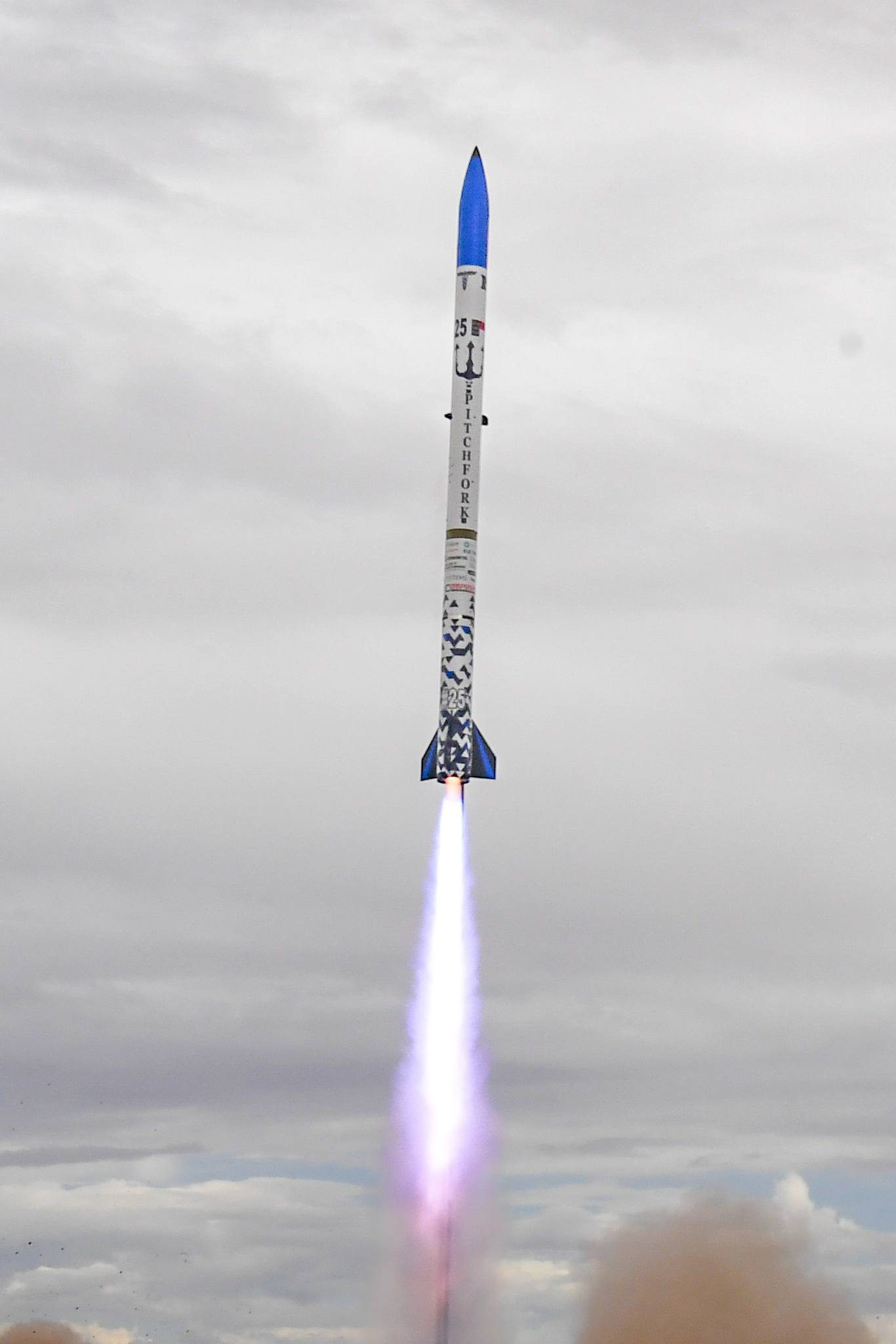

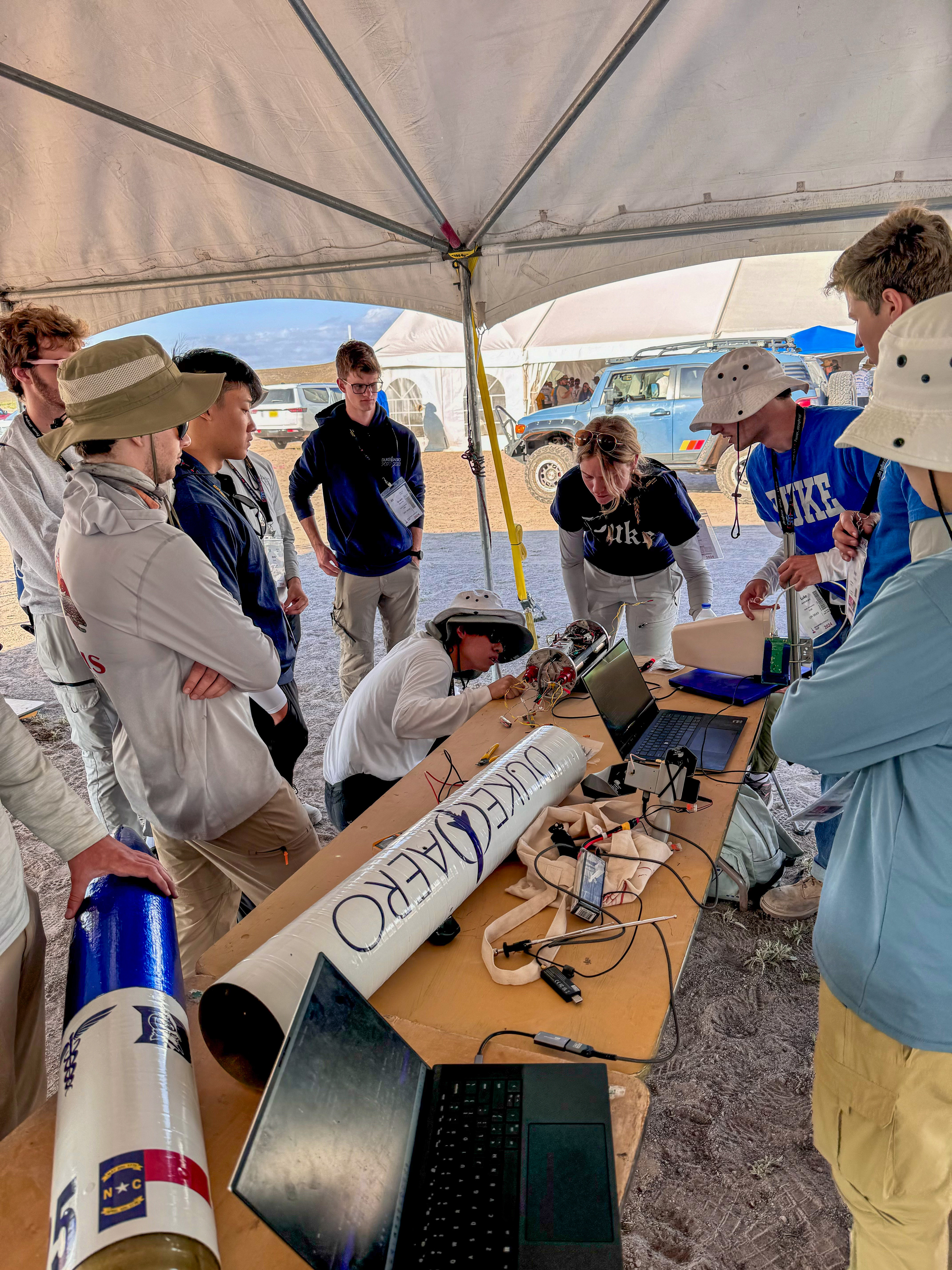
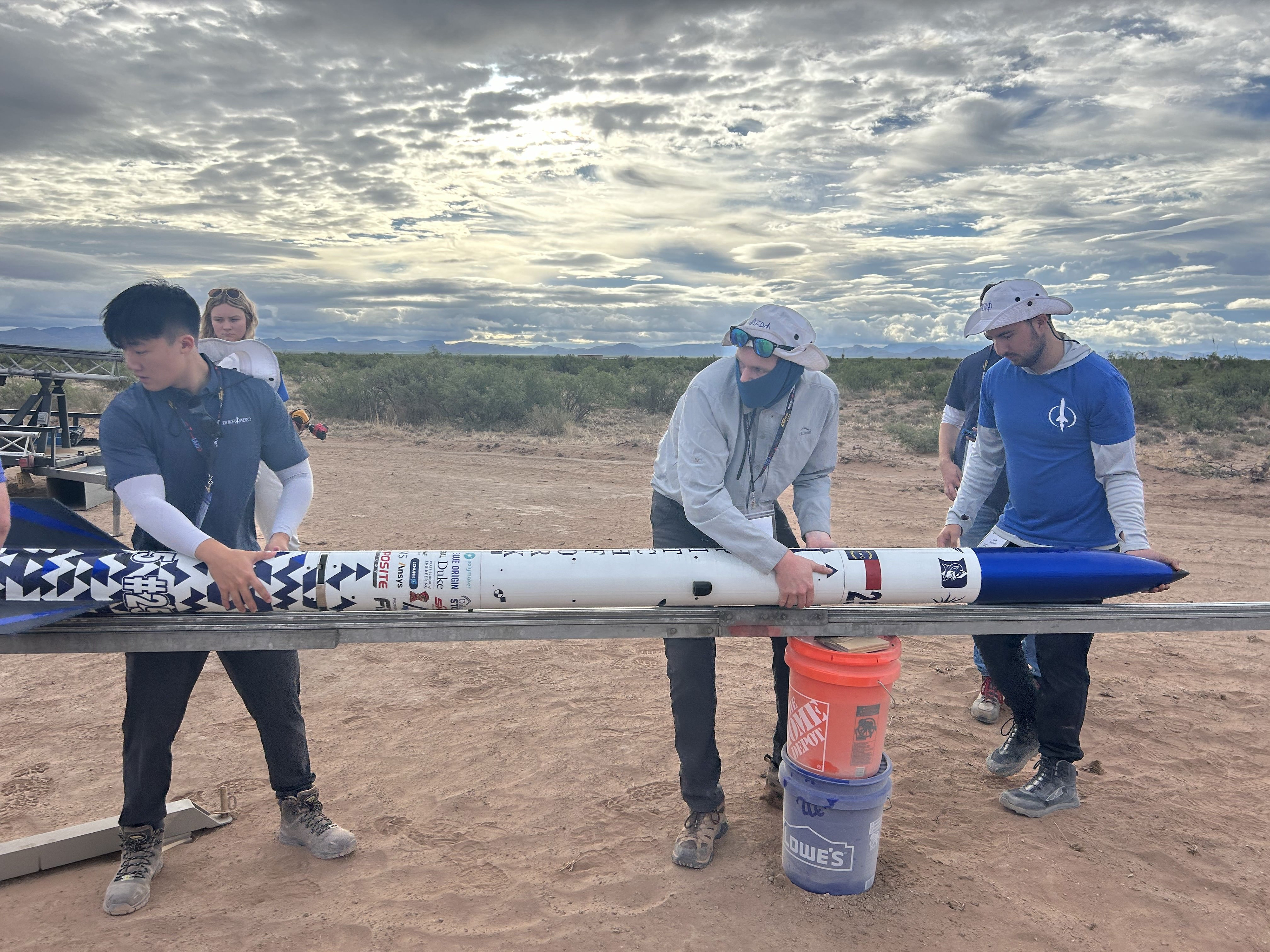
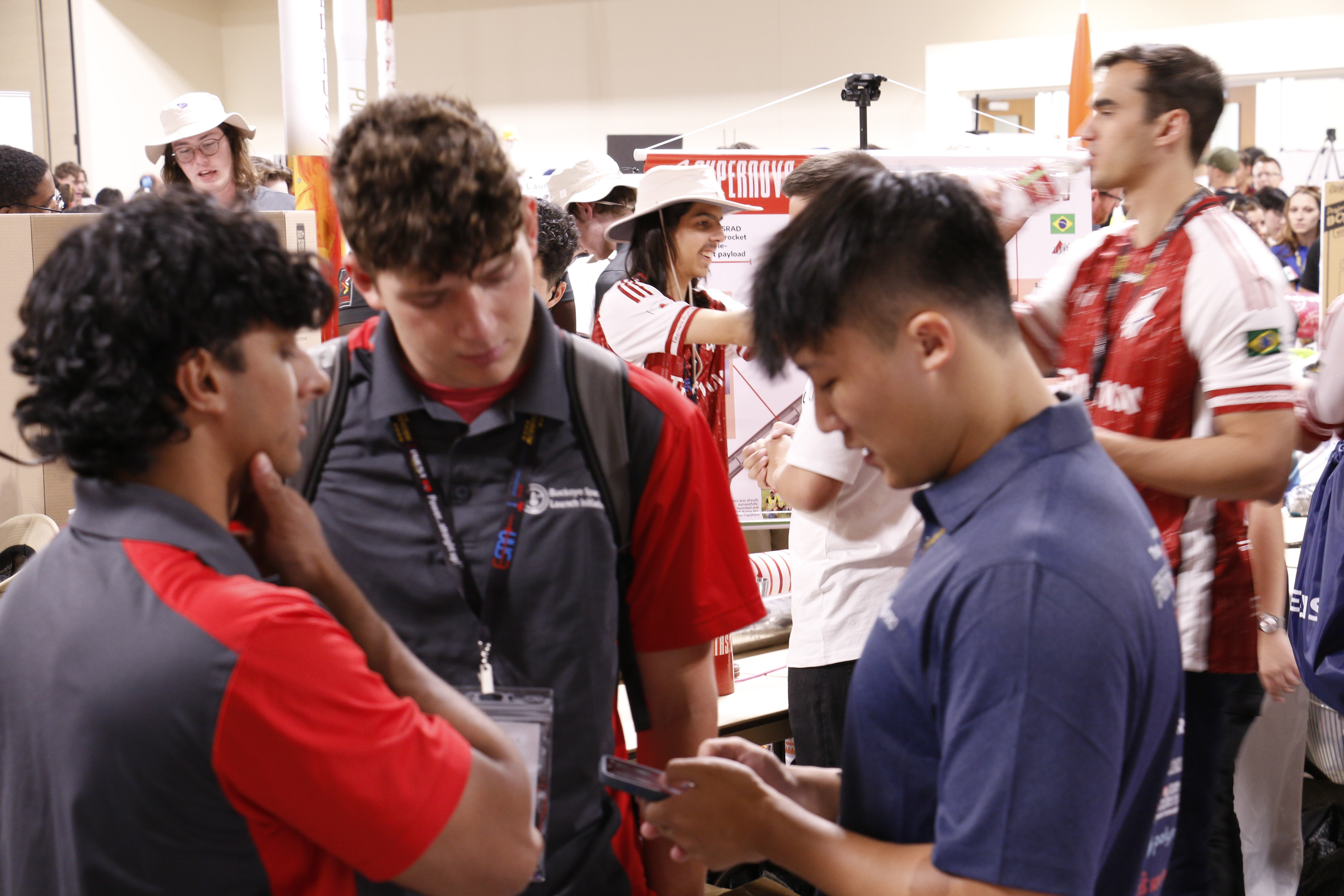
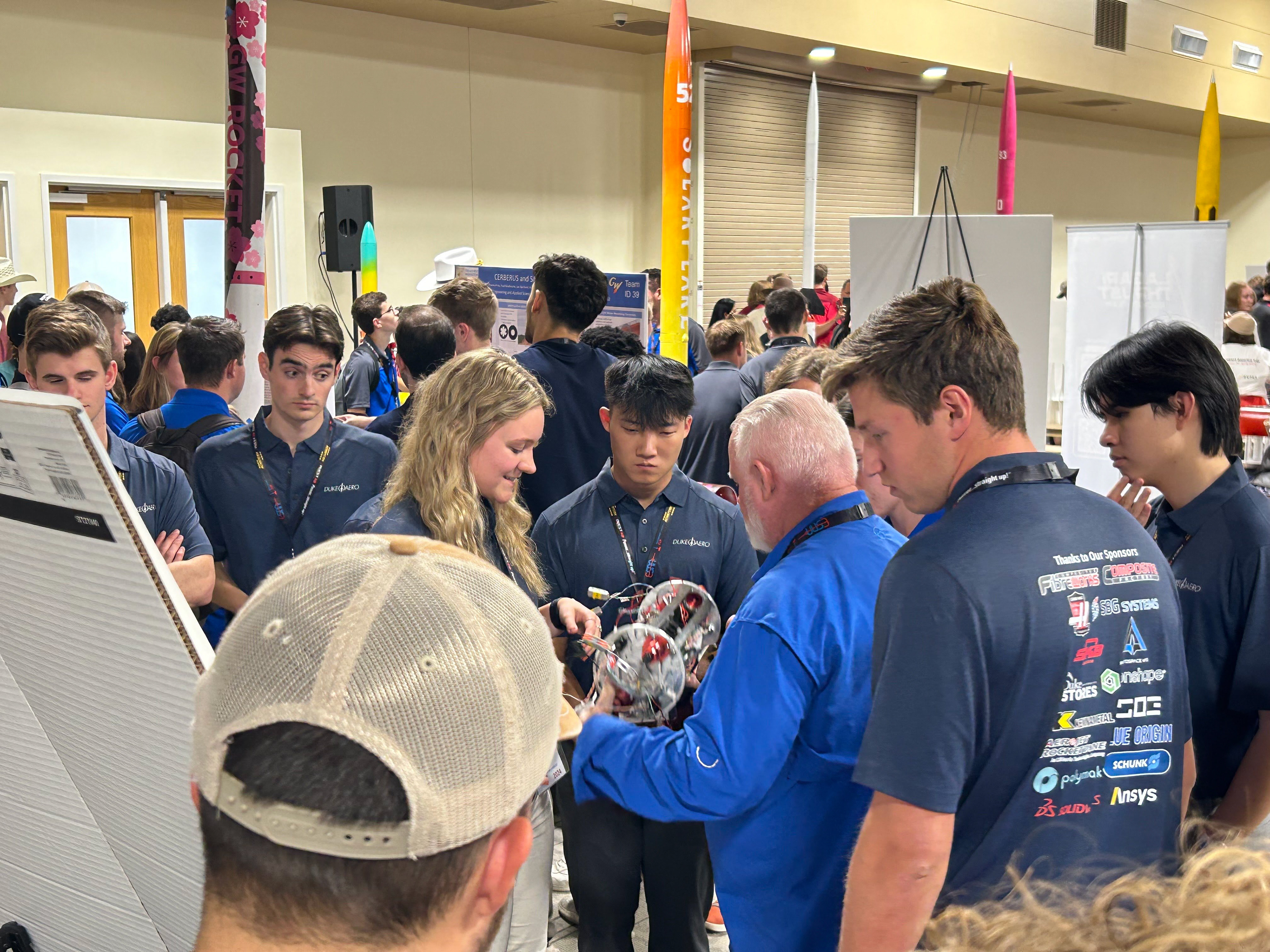
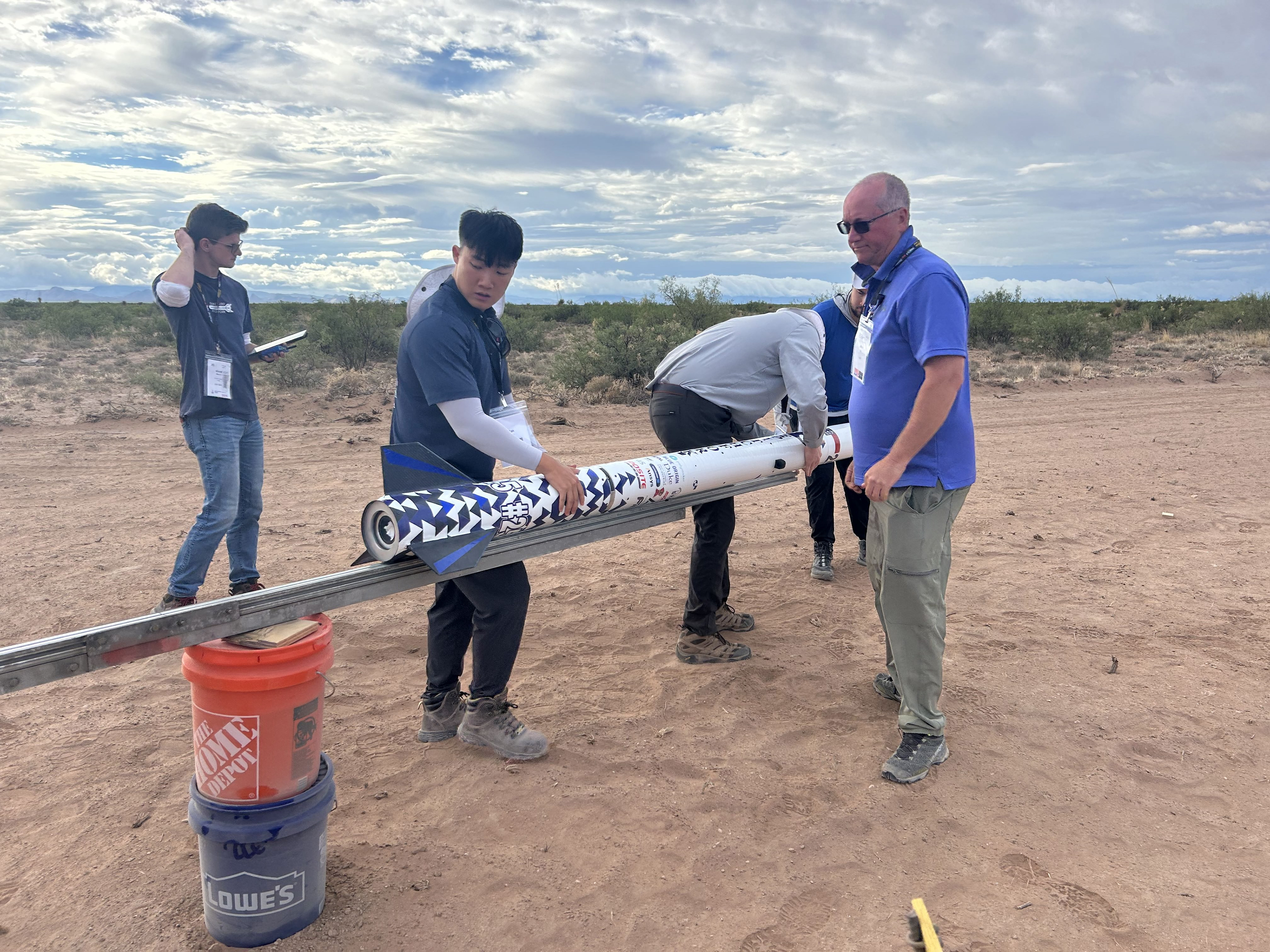
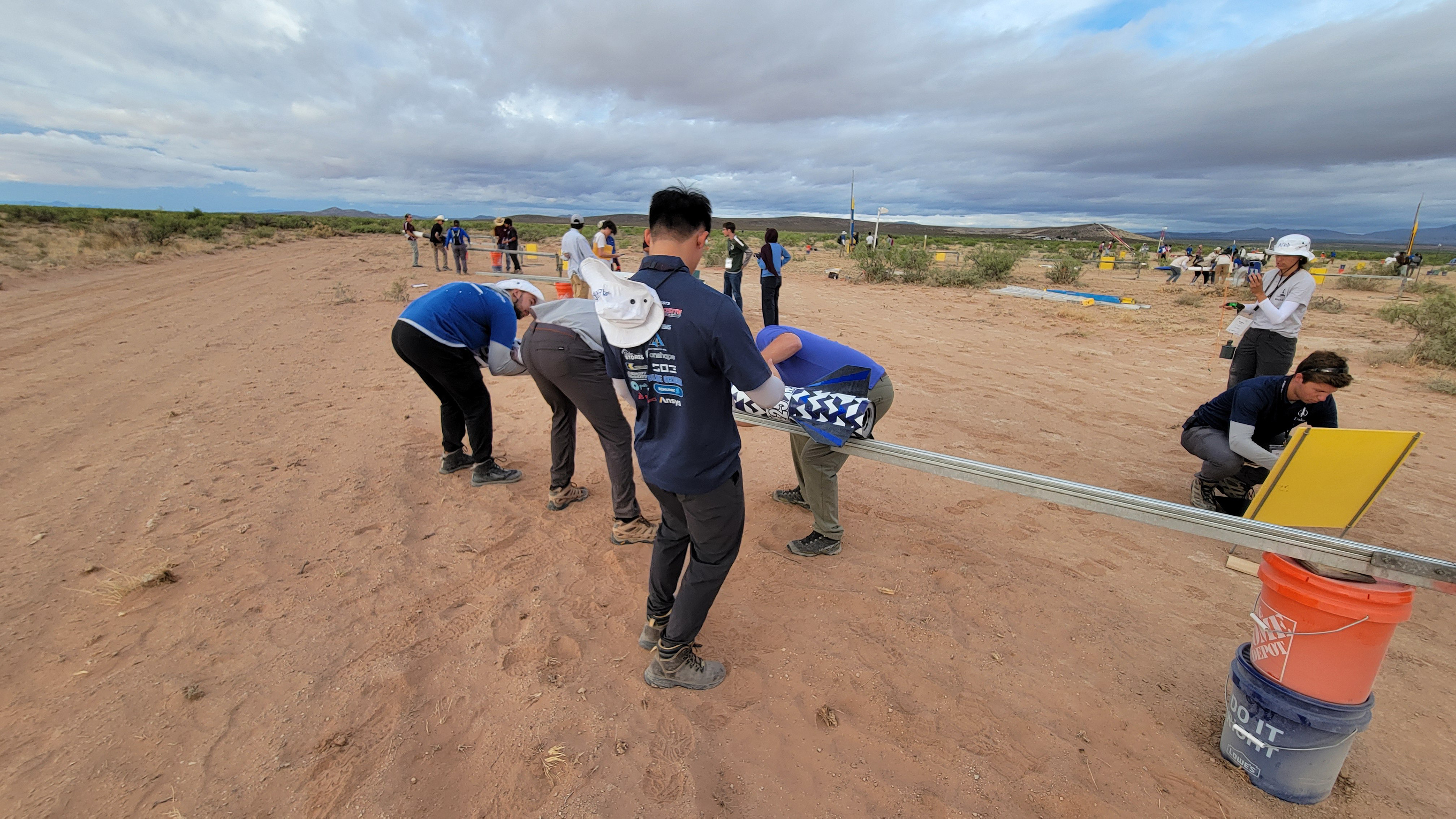
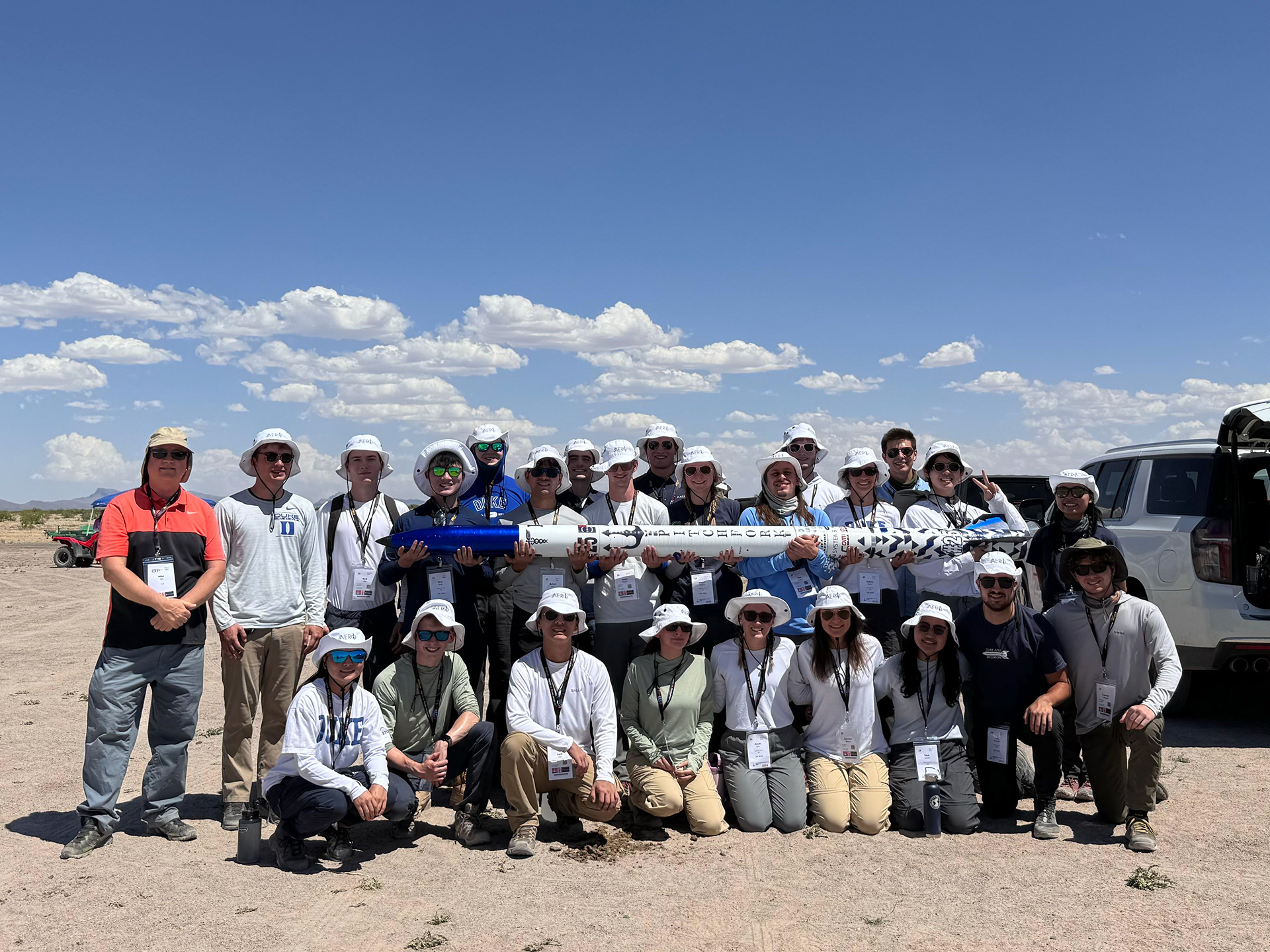